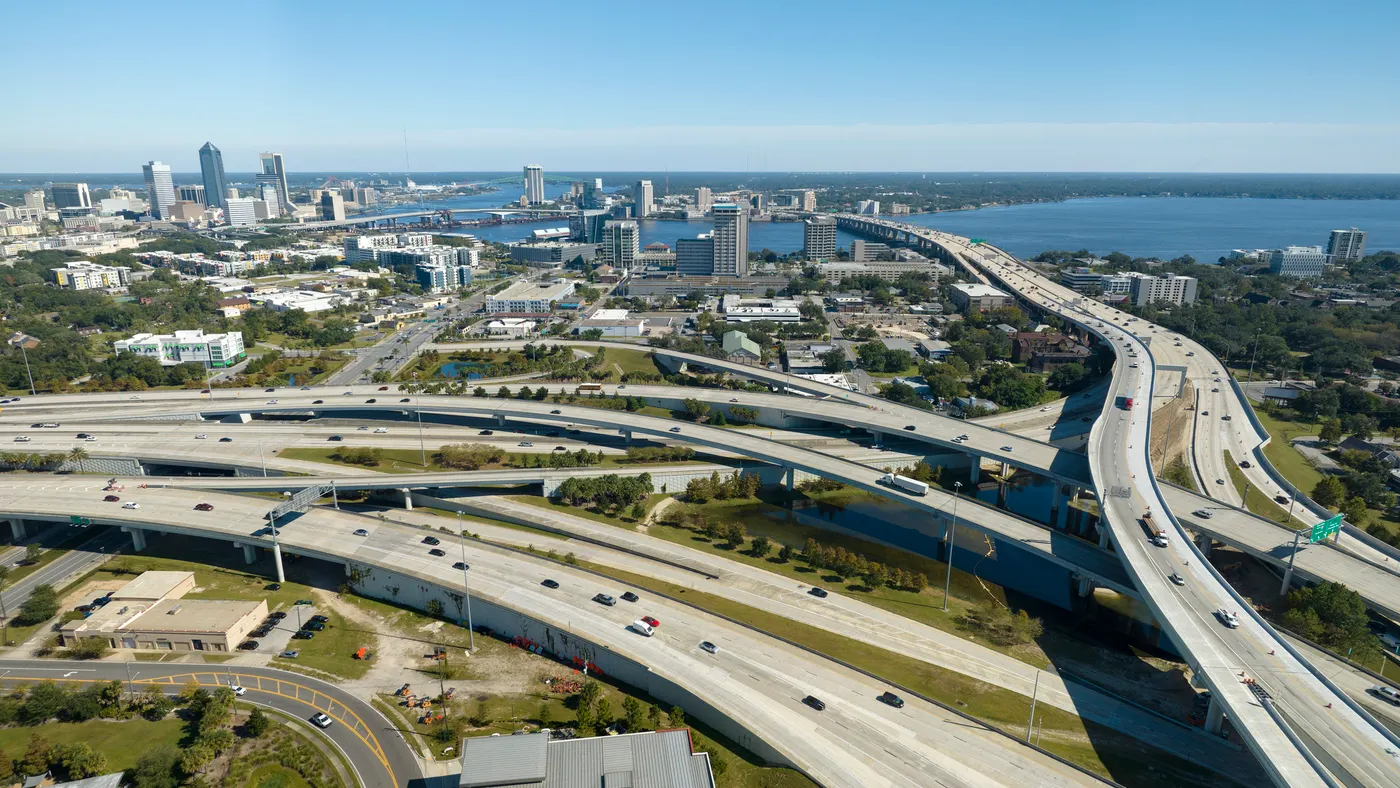
Why building US highways is so expensive
The U.S. overspends on its transportation infrastructure compared to its international peers, and a team of university researchers wanted to understand why.
Their investigation found that lack of DOT staff capacity and a dearth of contractor competition in the market are key drivers of high project costs.
State and local governments expended $266 billion on highways alone in 2022, and on a per-project basis, that spending is over three times as high as other upper- and middle-income countries, the researchers found. It’s not just American road projects that are expensive: A 2021 Eno Center for Transportation study found U.S. rail projects cost more and take longer to complete than similar builds in other countries, especially those that involve extensive tunneling.
To suss out why highway construction costs are so high in the U.S., Zachary Liscow of Yale University, Will Nober of Columbia University and Cailin Slattery of the University of California, Berkeley, surveyed infrastructure procurement practices, talked to state DOT employees and road builders and collected and analyzed project-level data across the country.
They presented their 2023 paper, “Procurement and Infrastructure Costs,” last month at Washington, D.C.-based policy think tank Brookings’ 2024 Municipal Finance Conference.
The paper is the first to use cross-state evidence to understand what role procurement practices play, according to the researchers. They found project quality and prices are not uniform across the country: There is notable variation in procurement practices, costs and road quality across the 50 states.
Lack of DOT capacity drives up costs
Simply put, the researchers found better staffed DOTs build roads more cheaply.
There has been a “striking decrease in state DOT employment over the last 20 years, especially in the wake of the Great Recession,” the authors found, and many state DOTs now have limited capacity. One result of this situation is an increased reliance on consultants when building projects, which is correlated with higher costs.
Indeed, the researchers found a one standard deviation increase in reported consultant costs is associated with an almost 20%, or $70,000, increase in cost per lane-mile. States with higher DOT employment per capita have lower infrastructure costs: A one standard deviation increase in DOT employment per capita is correlated with 16% lower costs.
Survey respondents attribute a lack of detail in project plans to both a lack of time or experience of DOT engineers, and the use of consultants. When there is not enough specificity in plans, the risk to the contractor increases, which drives up bids. Plus, whenever the scope of a project changes, this initiates a costly and time-consuming renegotiation process, which is a major contributor to cost hikes.
“We find that DOTs that provide more details at the time of the bid-letting have lower costs, while states with more change orders, which are often the result of poor planning, have higher costs,” according to the study.
The researchers found one additional change order correlates with $25,000 in additional cost per lane-mile at the mean, while costs are lower when the DOT provides both detailed project plans and predicted unit costs.
The researchers also collected data on individual California DOT engineers and found that a substantial amount of the variation in the cost of a resurfacing project can be explained by which engineer is assigned to it. Replacing an expensive construction engineer, at the 95th percentile of the cost distribution, with a median engineer would reduce costs by 5.3% on average, which works out to $24,000 per mile or $220,000 per average project.
Lack of competition leads to expensive projects
Road projects also suffer from a lack of competition among builders, a factor procurement officials and subcontractors alike frequently cited to the researchers. Most states have fewer construction firms than a decade ago, and most state DOTs report doing little bidder outreach.
A 12% increase in bidder outreach is correlated with a 17.6% decrease in costs, which translates to a mean decrease of $65,000 per lane-mile and $1 million at the project level.
Researchers also examined external data on the highway construction industry, and found that concentration in the industry seems to be rising.
“Most states have experienced a loss of construction firms, and an increase in size of the remaining firms, in the last 10 years,” according to the paper.
They found that an additional bidder on a project is associated with 8.3% lower costs, or a savings of about $30,000 per lane-mile, which translates to $460,000 for the average project.
Lastly, the researchers found that limits on the amount of work that can be subcontracted is also correlated with higher costs.
“Restrictions on subcontracting can decrease competition by limiting the set of potential prime contractors that can complete the project,” the authors wrote.