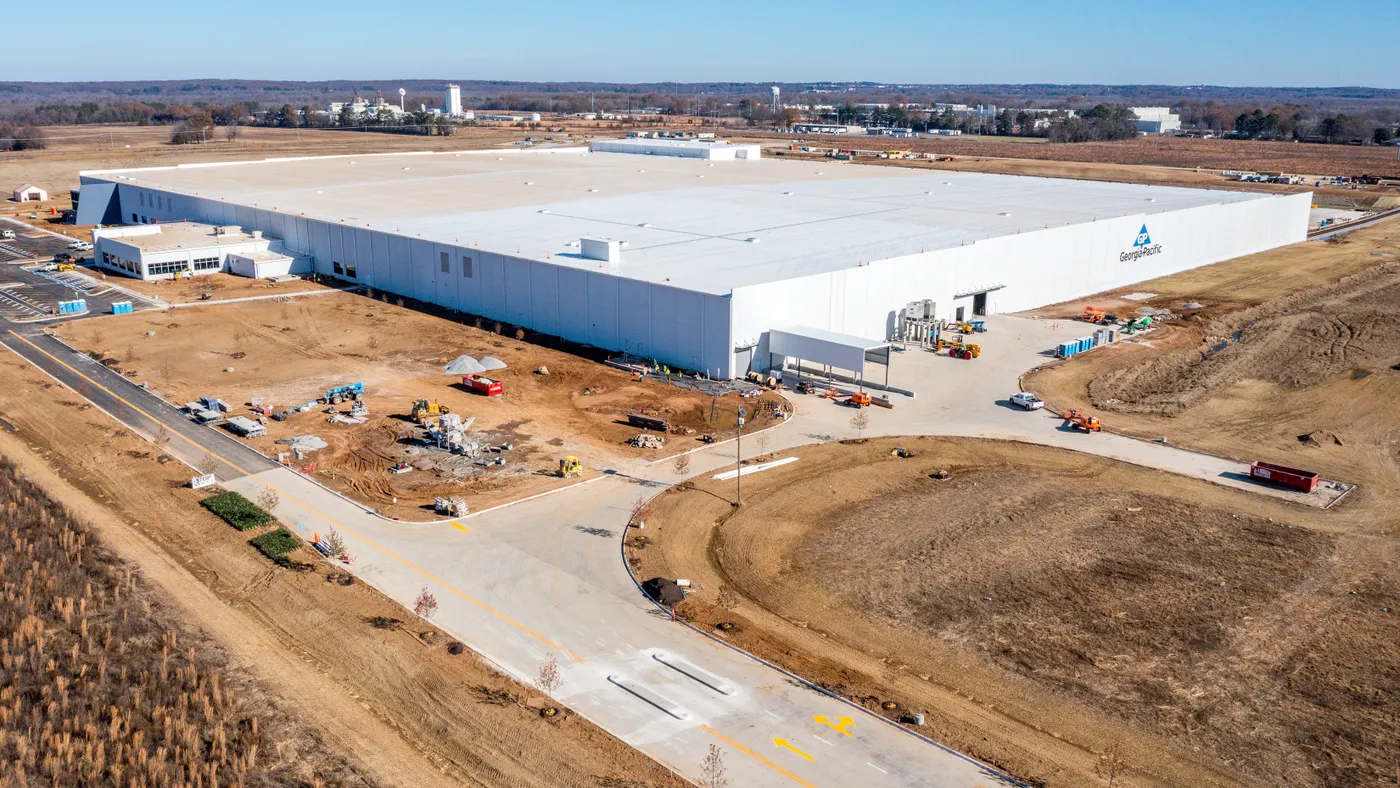
Why contractors are still all in on manufacturing projects
Since reaching record highs in May 2023, the manufacturing construction boom has shown signs of fading.
Although today’s manufacturing construction activity still dwarfs pre-2022 levels, starts in the sector have started to slow, according to Dodge Construction Network. That led The Wall Street Journal to question whether the segment has slipped into a slump.
But while those signals could portend weakness ahead, most contractors have remained unfazed.
“The manufacturing construction sector is very busy, and from discussions with our clients, we do not expect to see a slowdown any time soon,” said Andrew Ahrendt, national director of manufacturing at PCL Construction, an Edmonton, Alberta-based construction firm with U.S. headquarters in Denver. “We’ve barely scratched the surface.”
Slowdown emerges in manufacturing construction activity
General contractors in the space insist they do not feel a slump. In fact, they still foresee an acceleration in activity in the near term.
For example, along with PCL, JE Dunn plans to stay busy on manufacturing jobs in 2024. The Kansas City, Missouri-based company will deliver Dongwha Electrolyte’s first project in North America, a $70 million electric vehicle battery production facility in Clarksville, Tennessee, as well as a $425 million manufacturing plant for Georgia-Pacific’s Dixie brand of consumer goods.
“We continue to see a demand in the market for large capital projects and our counterparts at architecture and engineering firms remain busy with new project inquiries,” said Brent Strength, senior vice president and manufacturing market leader at JE Dunn. “Manufacturing construction in 2024 should surpass 2023. Contractors have a healthy backlog from previous years, and there is a lot of Inflation Reduction Act, CHIPS Act and similar dollars being spent right now.”
Chicago-based Clayco also expects to remain busy with advanced manufacturing construction this year. The company recently won awards to build Rivian’s $5 billion EV plant in Stanton Springs, Georgia, as well as Entek’s $1.5 billion manufacturing campus in Terre Haute, Indiana.

“I do think that the advanced manufacturing segment is definitely continuing to see significant investment, and I think that’s going to continue to expand at very high rates in 2024,” said Anthony Johnson, president of the industrial business unit at Clayco, a Chicago-based construction firm. “We’re going to see a ramping up of actually more capital projects in 2024 than we did last year.”
2023 issues linger
Despite the optimism, contractors working in the manufacturing space face specific challenges as well.
Robust manufacturing starts in 2023 stretched procurement timelines for many materials across the board, namely microchips, HVAC equipment, electrical switchgear and fabricated millwork. Additionally, countries in Asia and elsewhere produce many of the essential materials used in EV battery technology, like copper and nickel, said Strength.
That could slow progress, as the integration of this equipment into U.S. building codes and standards requires a uniquely qualified design-build team. Issues with procurement and adhering to U.S. code regarding EV construction, especially for first-time builders, can add months to the overall timeline of the project lifecycle, said Strength.

“Lead times for key equipment are still an issue that we spend a great deal of time mitigating,” said Strength. “Speed to market is still a priority. It is critical to work with a firm who understands how to plan ahead and navigate these challenges.”
Nevertheless, the flattening out of interest rate hikes, the easing of inflation and rising consumer strength should help bolster activity in 2024, said Johnson. He added while some uncertainty remains, the U.S. is in a much more controlled spot this year as it relates to inflation and interest rate hikes.
“I think all those stars are aligning to help provide some tailwind,” said Johnson.
Manufacturing construction activity to ramp up this year again
Labor woes
In 2023, builders constructed numerous phase one-type projects. This year, Johnson expects a similar second wave of related projects to break ground.
Additionally, for companies that experienced delays in finalizing their planning, financing or purchasing agreements in 2023, it is likely those projects will also break ground this year. For example, 16 manufacturing projects worth around $8 billion had their target start dates moved from the end of 2023 into 2024, said Richard Branch, chief economist at Dodge Construction Network.
That will amplify an already deep-rooted challenge within the industry.
“In 2023, there was certainly a strain on craft labor throughout the United States,” said Johnson. “That’s only going to get exacerbated this year because you have that wave of projects, similar to what you had in 2023, but now you also have a whole new wave starting this year too.”
Notable projects that were delayed last year include Scout Motors’ $2 billion plant in Blythewood, South Carolina, and American Battery Factory’s $1.2 billion factory in Tucson, Arizona.
“I think there are some risks here, particularly because that access to labor could undermine this forecast,” said Branch. “That’s coming at a time also when EV demand seems to be slowing down.”
TSMC recently delayed the production timeline at its second factory from 2026 to either 2027 or 2028, due to a shortage of skilled workers and challenges securing U.S. government funding, according to Chairman Mark Liu. The firm had already postponed production at the site’s initial factory from 2024 to 2025.

Still, many projects funded by tax credits from the Inflation Reduction Act are already in design, and are likely to continue to move forward as supply chains have already pivoted to rely on these new models, said Ahrendt. That momentum will keep general contractors that work in the space busy for the considerable future, said Strength.
“The pace and amount of capital investment may ebb and flow,” said Strength. “But we believe momentum will continue to move in a positive direction in the years to come.”