Trent Mostaert says he has the coolest job in the world.
Over the past few years, the vice president of industrialization for Minneapolis-based Mortenson has been keeping an eye on physical artificial intelligence. That’s the area of how physical and digital tools can be married and optimized to support workers in their particular environment.
Mostaert’s particular expertise comes in the field of industrial-scale solar installations, where AI-powered robots have been creating big inroads.
Here, Mostaert talks with Construction Dive about what he’s learned in the last two years of tech advancement, his people-first mentality when it comes to process adoption and a warning for those who try to innovate too quickly.
Editor’s Note: This interview has been edited for brevity and clarity.
CONSTRUCTION DIVE: What should people know about physical AI?
TRENT MOSTAERT: Every task has a heartbeat.
On a solar project, you're distributing a pile every five seconds. At 30 piles, you need to go and get another load. It’s a cycle of five seconds, five seconds, five seconds, and then five minutes. That’s the heartbeat of that simple task.
At the end of every task, you’d get two pieces of information — you would know what your production was, and you would know how many craft hours it took to do.
Now, as we've integrated more digital control systems into our equipment, each piece of equipment might generate 10 million data points.
So what do you do with all that data? How do you organize it so you can look at what the heartbeat should be of each activity, and optimize across your whole fleet or crews? How do you make sure everything is operating as planned?
The biggest thing is, once the heartbeat stops, once it flat-lines, who and when should somebody be notified? And how are they reacting to that issue? And as AI gets more sophisticated, how can we automate with AI?
What are some of the lessons you’ve learned about tech?
I’ve always been excited about lean construction, but I felt like most of my focus would be more on creating training and equipment tools, automating them, and trying to figure out how to make AI work with them.
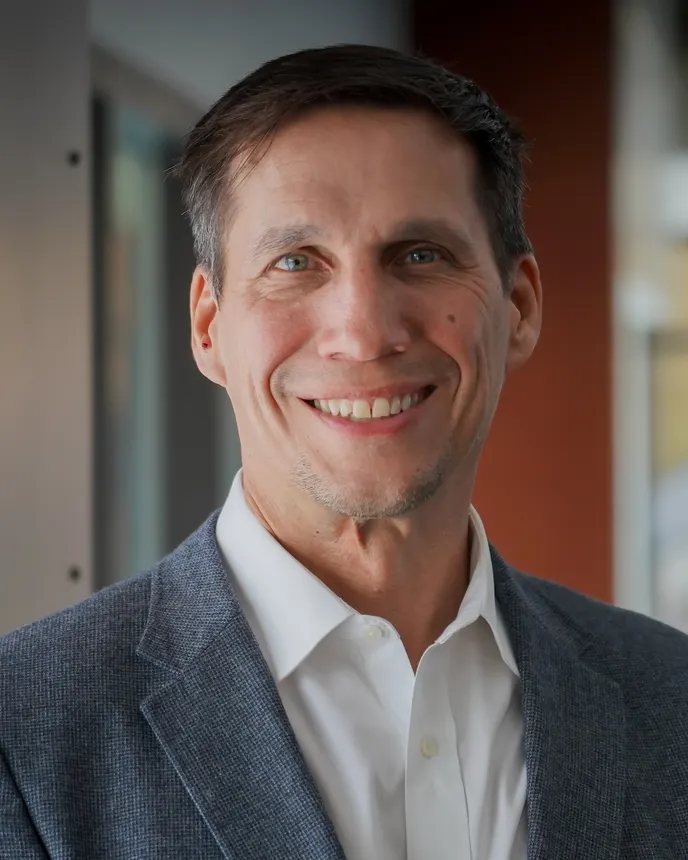
In reality, what I learned was that we really needed to go back and focus on our people, put people at the center and understand the work. Our best ideas always come from our field.
So it was more of an embracement of the field, how things happen in the work, and how we make the work easier for our craft members by developing solutions that meet their needs.
You attended BuiltWorlds Venture West conference and spoke about physical AI. What is that?
The concept of physical AI is interesting.
As we've been industrializing, for us, it's really the fusion of the physical world — for us, meaning the equipment and tools and the work environment — with the digital world. That includes everything that’s coming up, the mega trends, and then also fusing that into the human world, or the bio world.
So, fusing the biohuman systems, the physical world and the digital world is what we’re doing with I4, or the fourth industrialization, which is the fusion of all those systems.
When you think about physical AI, that’s just creating intelligent solutions with the physical world, which is mostly equipment.
We have excavators on our jobsites. People have been adding intelligence to them, such as automation and sensors and control systems.
How does Mortenson plan to adapt to this new age of industrialization while still keeping a human-centered approach?
When you think about implementing physical AI in the world, you need to follow an order.
First, you must start people at the center of the work and make the work easy. Second, you have to implement better processes, tooling and equipment. You need to take the waste out of the system. Otherwise, you're just automating the wasteful process. Once you’ve done all that, then you can start to automate and integrate AI into the system.
What takeaways have you gained from following that process?
You should never automate without understanding the technology. If you don't understand the technology, you're going to end up with a lot of problems implementing technology that's not going to be reliable. If you don't understand it, it's hard to keep it working.