American River Constructors, a joint venture of Granite Construction and Pleasanton-based California Engineering Contractors, has played it safe at the $131 million American River Bridge project in Sacramento, California.
As the job has progressed over the last three years, workers have taken a 20/20/20 approach, pausing their work every 20 minutes to perform a 20-second scan of the area 20 feet around them. That has resulted in just one recordable injury — a broken right ring finger — over more than 100,000 hours worked.
In light of Safety Week, the team is holding an event today at the project, where in addition to 3D BIM models and de-watered coffer dams, crews have used a STCKY (Stuff That Can Kill You) hazard recognition program to help achieve the low injury rate. The job for Caltrans started in 2022, with completion slated for next spring.
Here, Watsonville, California-based Granite’s Project Executive Bob Mihal talks to Construction Dive about how the job came about, a permitting process that went unusually fast and steps that eliminated $85 million from the overall project cost.
Editor’s note: This interview has been edited for brevity and clarity.
CONSTRUCTION DIVE: The American River Bridge, which carries the I-80 Business/Capital City Freeway over the American River west of Sacramento, was originally built in 1954. What issues were emerging in the structure?
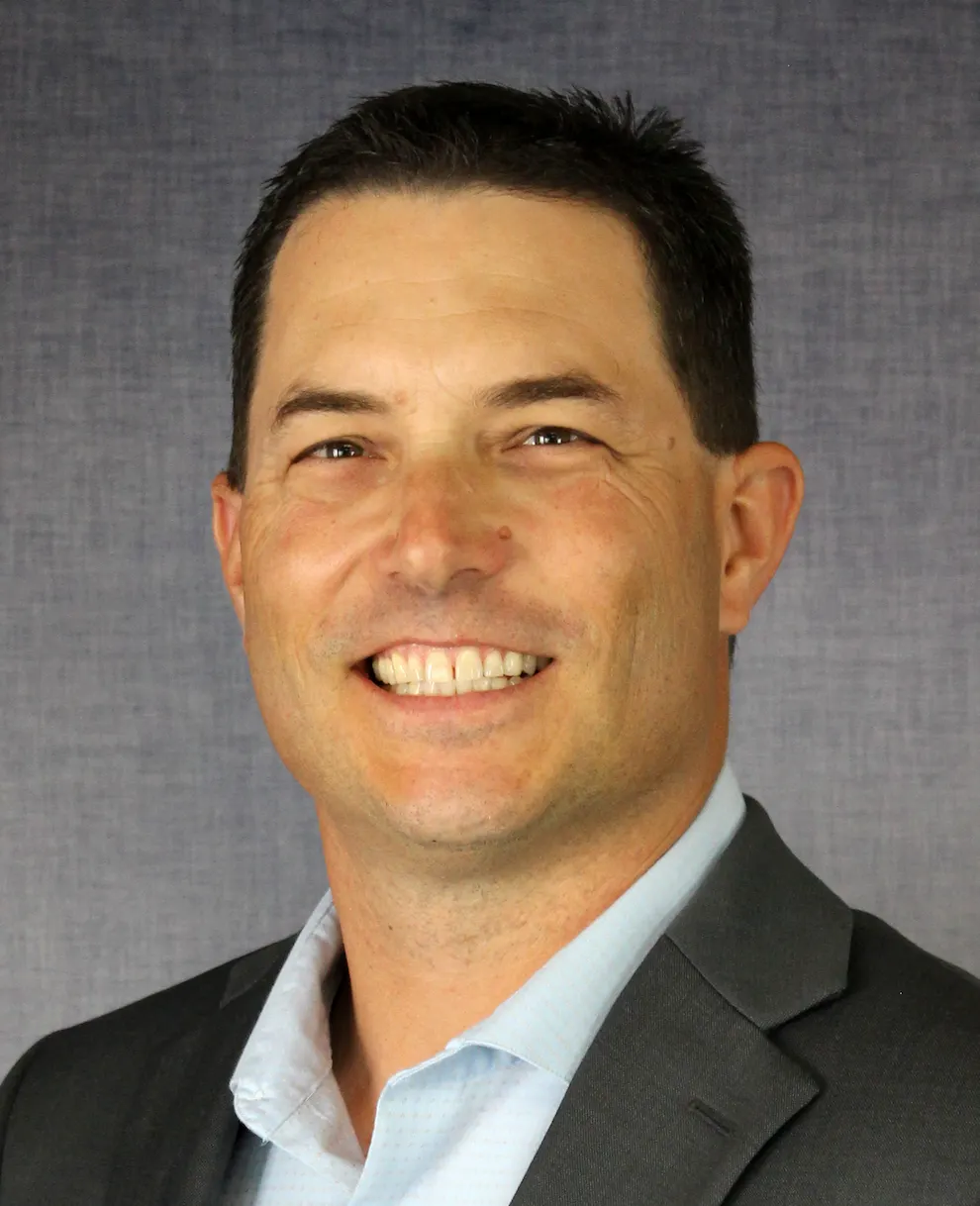
BOB MIHAL: The original bridge was built as two separate parallel bridges in 1954 with a center widening in 1964, and the bridge decks were showing their age. Due to the severity of the transverse and longitudinal deck cracks, concrete spalling and high corrosive chloride content in the concrete deck surface, the bridge deck needed replacement.
To accomplish the deck replacement, the superstructure was first widened to accommodate traffic during construction.
What were the biggest challenges on this project?
The substructure work for the deck widening started in the spring of 2022, and we anticipate overall project completion in the spring of 2026. There were several significant challenges, including work in an environmentally sensitive floodplain, coordinating with multiple environmental agencies as well as the U.S. Army Corps of Engineers, weathering the series of atmospheric rivers and associated flooding over the winter and spring of 2023 and the technical challenge of rehabilitating a bridge in halves that was originally built in thirds.
Access to the work is a constant challenge, with a barge fleet in the river, maintaining access roads and work pads through multiple winters and bringing material and workers into the center median between heavy flowing traffic on both sides during the first stage of deck reconstruction.
I understand the JV couldn’t work in the river from June to October. Why was that and how did you keep the job moving given those parameters?
From November through May, Chinook salmon and steelhead are actively spawning. During those months we were restricted in that we could not actively disturb the river or induce piledriving vibrations.
Outside of that window from June through October, we were permitted to work from barges and within the dewatered cofferdams. We worked around the restrictions using careful planning and aggressive scheduling.
Installing all the sheet pile cofferdams and bridge piling in the first season prior to the river window closing in October was a large undertaking, but critical for allowing pier construction to progress through the winter. Collaboration with the environmental agencies confirmed that working from barges and within the dewatered cofferdams was not considered “in-water” work.
Using barges for access in lieu of a conventional temporary trestle bridge was a significant time-saving measure that allowed us to complete the pile driving prior to the river window closing.
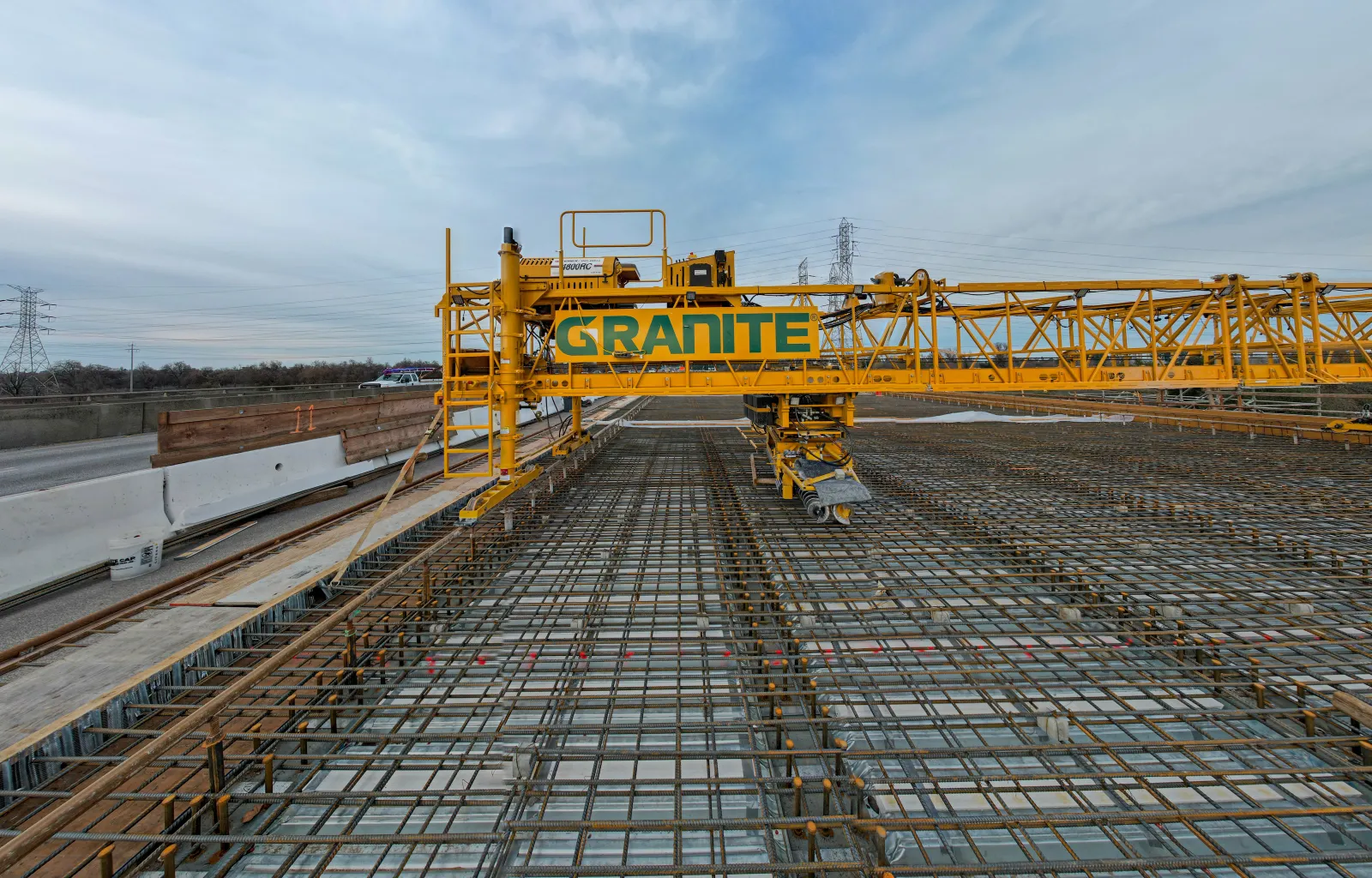
This contract was for a job in California, which is notorious for environmental and permitting delays, in a river with an active salmon run. Yet you were able to get it permitted in just 12 months. How did you pull that off?
This was a big success for the collaborative construction manager/general contractor process on the project. Our environmental permitting experts worked closely with the Caltrans environmental team and collaborated with the various permitting agencies to quickly communicate the project work plans and address any concerns prior to the formal permit applications. This allowed rapid permitting approval and minimized the typical back-and-forth process.
Why is the construction manager/general contractor contract significant, and how did it help in making this job a success?
Unlike traditional project delivery, where a design is completed before the owner selects the contractor, in a CM/GC project, the owner brings in the contractor toward the end of the preliminary design phase.
The contractor and designer then work together, under contractual coordination requirements, to complete the final design phase. In the process of working through the final design, they can work together to identify more opportunities for savings and flexibility.
In the case of the American River Bridge project, one with significant complexity and multiple stakeholders, collaborative contracting has been crucial for project success.
Early permitting, aggressive scheduling and collaborative problem-solving allowed construction to start two years early and has kept the project on time and on budget even with the significant technical and environmental/flooding challenges.
In addition, the collaborative innovations developed during design and construction planning have reduced the project cost by more than $85 million.
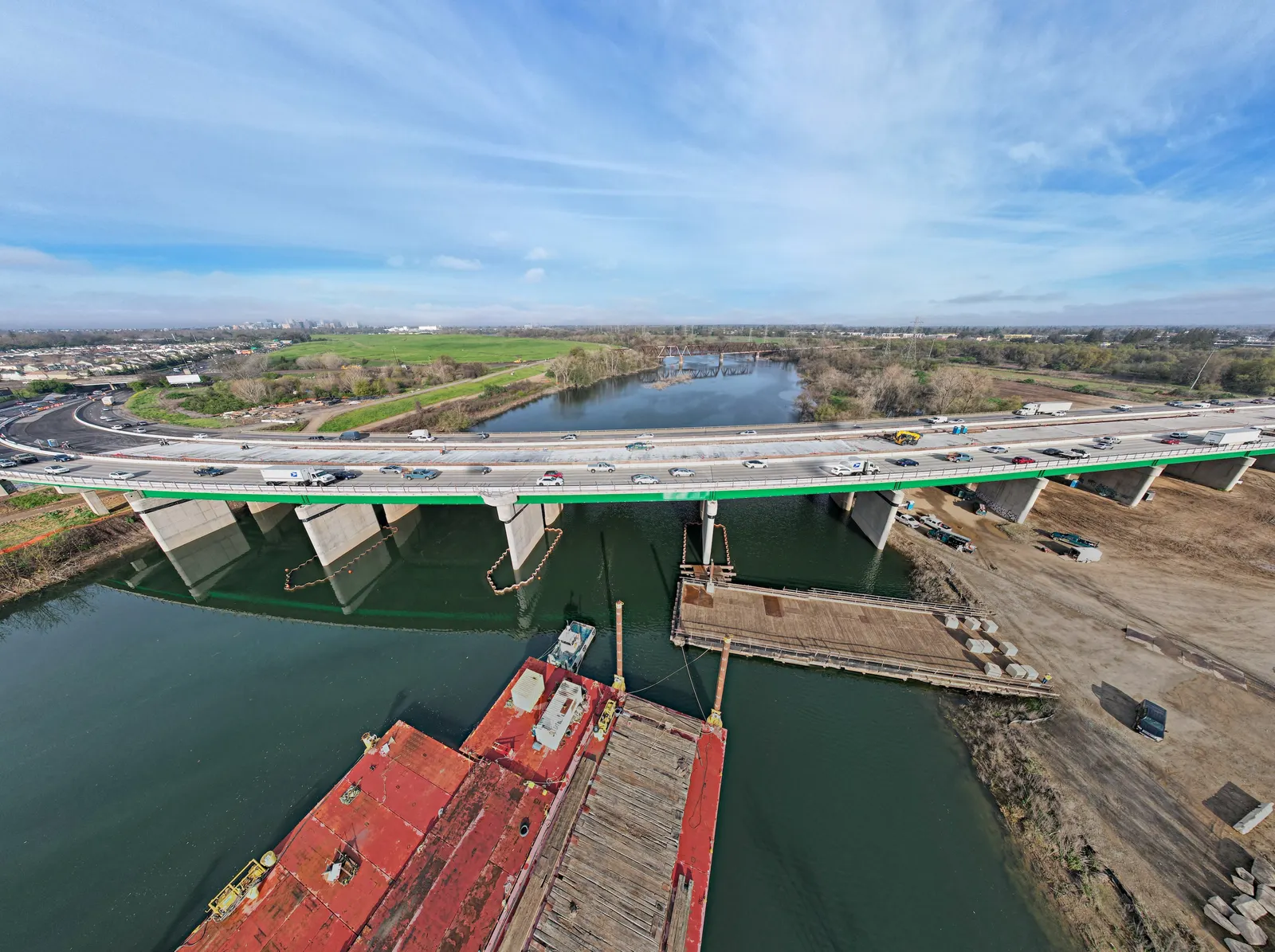
This project is currently nearing completion, but Granite has several other infrastructure projects that are ongoing. How has the funding environment changed this year?
Work on this project is ongoing, and we anticipate overall project completion in the spring of 2026. We see many strong opportunities in the market despite macro-economic uncertainties, and the federal infrastructure bill continues to support growth in construction opportunities.
Any other details you’d like to discuss?
The use of 3D modeling brought innovation — Caltrans usually just gives us design drawings. We took the design and made a 3D model and used it for survey and highly accurate field layout. This reduced requirements for survey and provided other constructability benefits — everything fits better.
Any time you build bridge foundations in the river, you impact the river. We decided to work off of barges instead of a trestle, which would have basically required building a temporary bridge — and would have had significant environmental impacts.
Dredging the river to create space for barges had lower impacts, saved time and was preferred by the environmental permitting agencies. This had a real benefit in 2023 during the big floods resulting from the atmospheric rivers we experienced; a temporary trestle could’ve been swept away.
Instead, we were able to rapidly move the barges and equipment to higher ground and avoided both equipment loss and environmental damage.
The new bridge will provide a multimodal connection between downtown and eastern Sacramento, including a Class 1 bike path that connects to existing bike routes.